TOJIRO OPEN FACTORY
1.Move on to ATELIER after FACTORY.
2.Factory is not operated during 12:00-13:00 and 15:00-15:10.
3.Pictures and videos are allowed, but flash is prohibited in order to avoid workers get blinded.
4.Please note, some machines may not be operated.
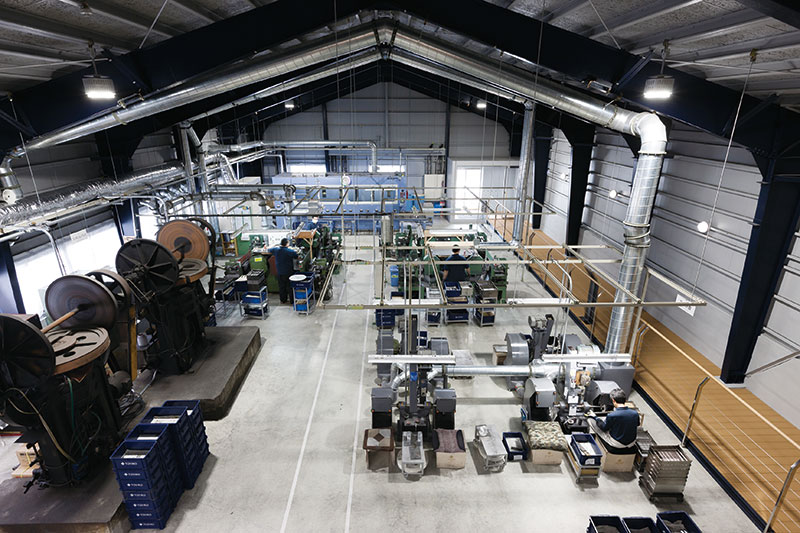
■ Manufacturing Process of Mass-produced Knives
(TOJIRO KNIFE FACTORY)
In this facility, part of our mass-production process can be observed, such as blade shaping by latest laser processor, heat treatment, and blade grinding by 3 pivot CNC grinder.
Our craftsmen/women make products with stable quality while combining latest technology and traditional technique.
1. Pressing(プレス)
3. Heat Treatment(焼入れ)
4. Grinding(研削)
5. Welding(溶接)
6. Bolster Polishing(口元研磨)
7. Blade Polishing(刀身研磨)
8. Hairline Finishing(目通し)
9. Cleaning(洗浄)
10. Marking(名入れ)
11. Handle Fitting(柄入れ)
12. Handle Polishing(柄磨き)
13. Sharpening(刃付け)
14. QC & Packaging(検品・包装)
* Friction Pressing(フレキションプレス)
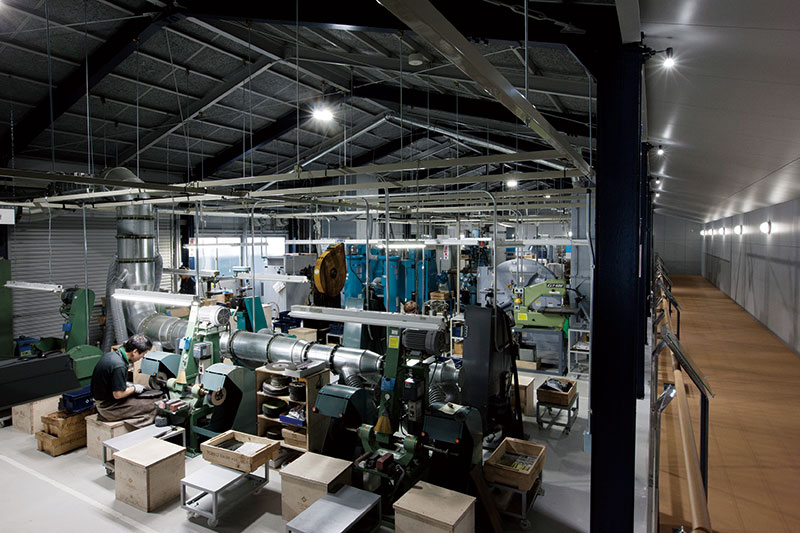
■ Manufacturing Process of Handmade Knives
(TOJIRO KNIFE ATELIER)
You may observe each procedure of our handmade knives in this facility.
From the tip of the blade to the end curve of the handle, using traditional Japanese forging technique, each one of them is thoroughly hand-finished by our craftsmen/women.
1. Forging(鍛造)
3. Shaping(成型)・Laser(レーザー)
4. Welding(溶接)
5. Heat Treatment(焼入れ)
6. Blade Grinding(刀身研削)
7. Sharpening(刃付け)
8. Blade Polishing(刀身研磨)
9. Cleaning(洗浄)
10. Handle Making(ハンドル製作)
11. Handle Polishing(柄磨き)
12. Carving(作切り)
13. Finish Sharpening(仕上げ研ぎ)
14. QC & Packaging(検品・包装)
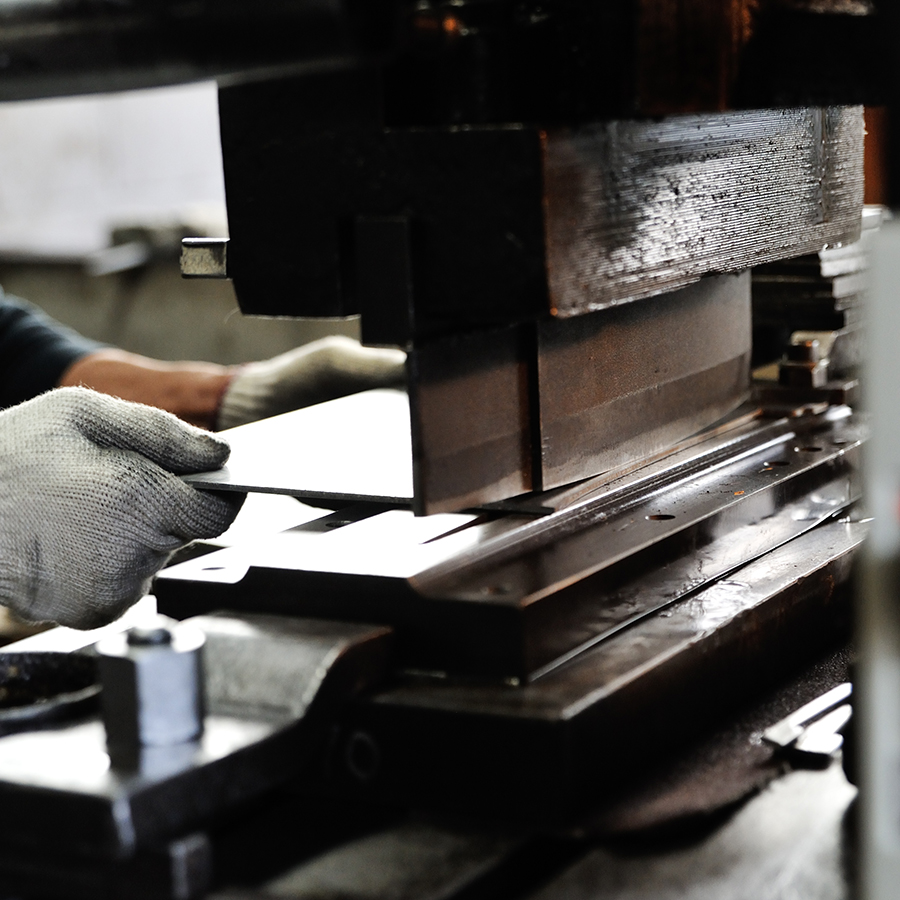
<Pressing>
First step of knife making is pressing the blade shaped piece of metal out of a sheet of raw material.
In order to minimize the waste, it is well conceived and thus the sheet looks just like cookie dough after pressing out.
Equipment: Press machine
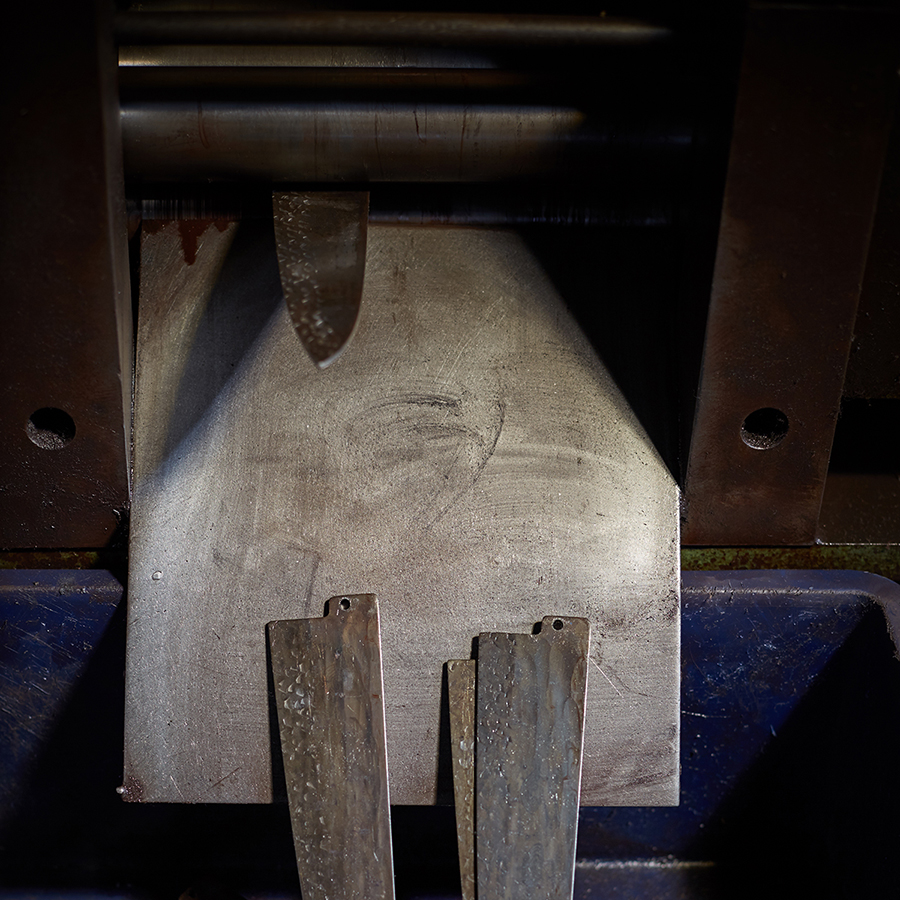
<Flattening>
The pressed out blade is warped due to the impact of pressing, so that it is necessary to flattened by going through the roller press before hardening process.
Equipment: Roller press machine
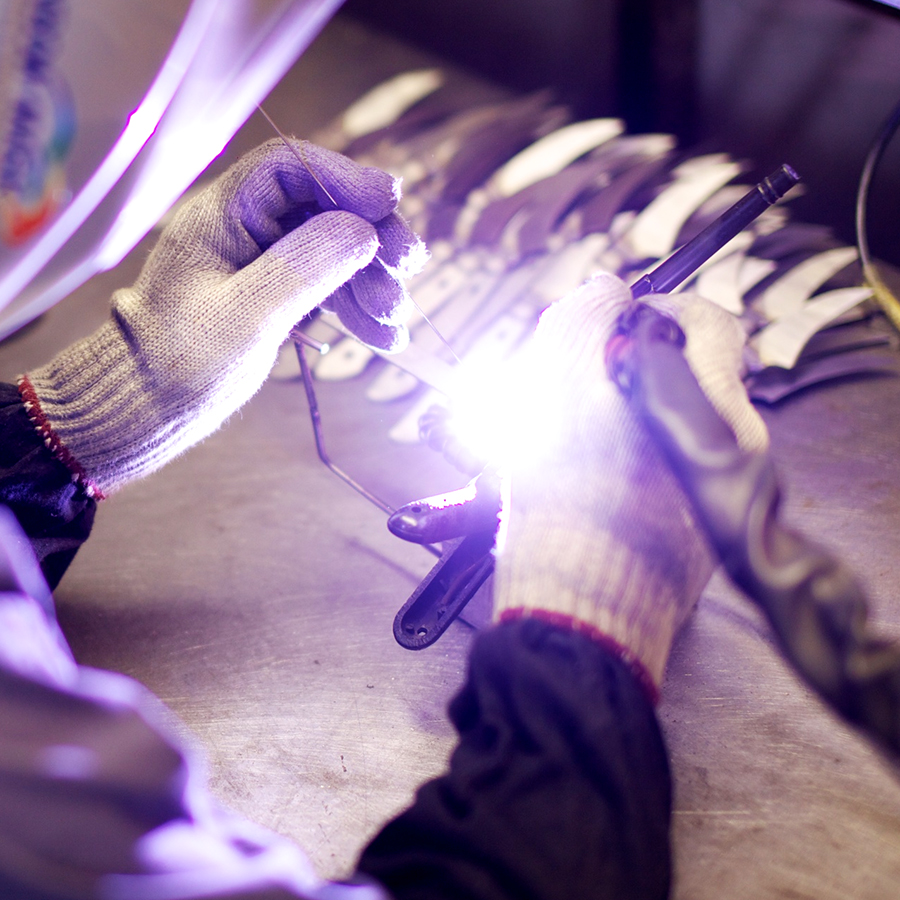
<Welding>
In order to obtain hardness, steel contains high carbon is used for blade.
Anti-rust stainless steel, on the other hand, is used for bolster.
These two different types of steel are welded in this procedure.
The metal part of the handle is called “bolster”.
Bolster prevents dirt and bacteria to be accumulated between blade and handle.
Equipment: Welding tools, Welding robot
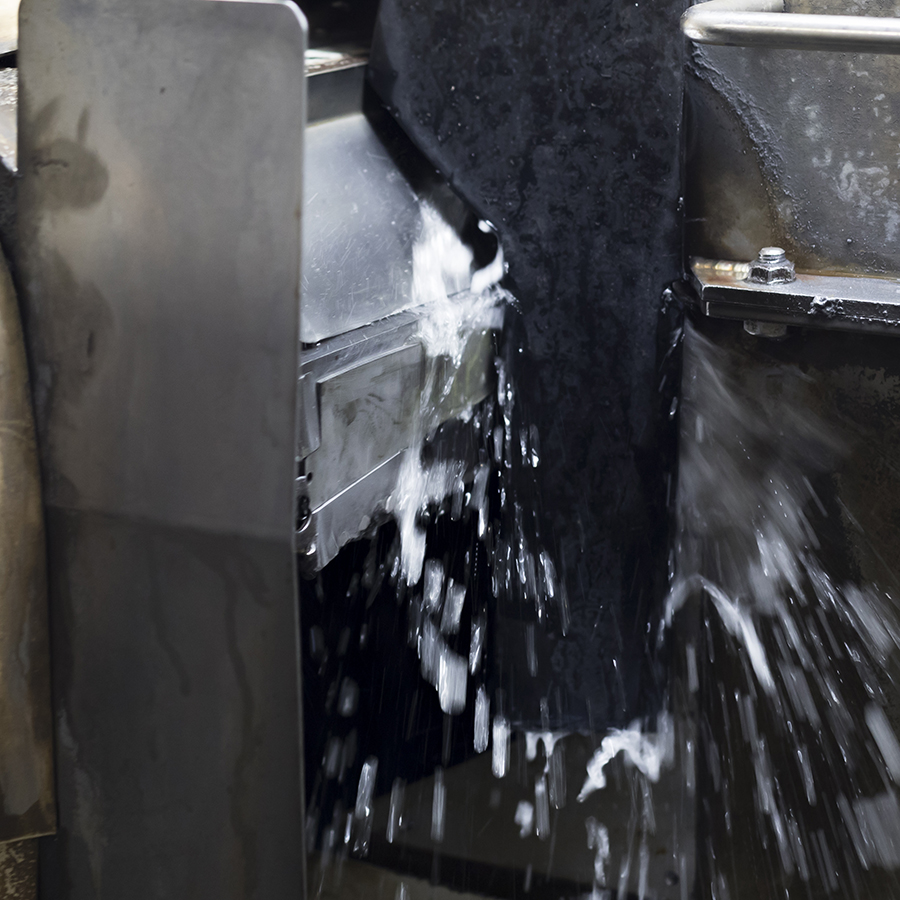
<Grinding>
Blade is ground and shaped into wedge-shape in this process.
In order not the blade to be annealed again, slowly and gradually, with appropriate amount of running water, it is ground by grinding wheel.
The blade is ground many times from different directions to form smooth curve toward the edge, which is so called convex edge.
Convex edge may not be as sharp as straight flat ground, however it is essential and effective to cut into food, and at the same time, for better edge retention.
If this process is failed, the edge can be very dull drastically after re-sharpening.
Equipment: Grinding machine, Sharpening wheel
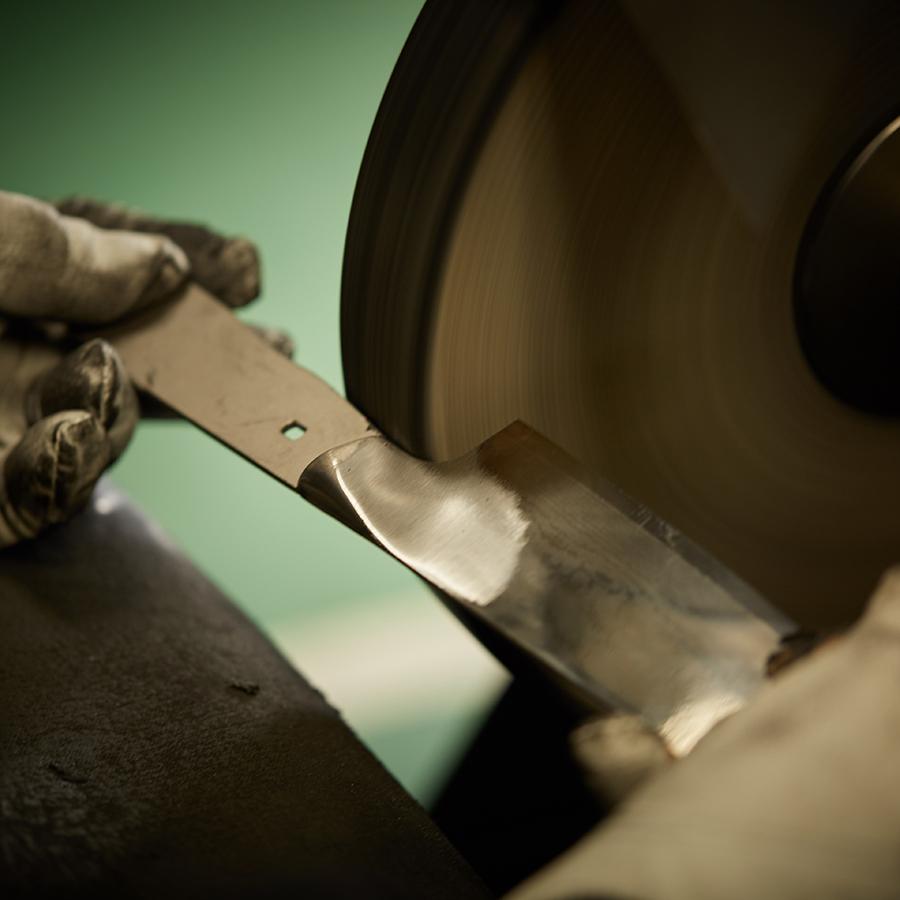
<Bolster Polishing>
Welded part of blade and handle is polished to form right shape of a knife.
By using different type of grinding stones and buffering machines, its surface is finished nicely and smoothly.
Since it requires very sensitive touch of work, it is done by hand rather than machine.
Equipment: Polishing and buffering wheel
<Blade Polishing>
In this process, blade surface is polished evenly and nicely in order to have a better look.
The blade which is relatively long can be polished by machine.
However, short blade, single bevel blade, or the one with particular type of handle, are hand polished one by one by craftsman.
Equipment: Polishing and buffering wheel
<Hairline Finishing>
Blade surface is glazed by hairline processing.
It is processed vertically or diagonally depending on the knife design.
This makes tiny scratches on the blade inconspicuous.
This is the final process of blade finishing.
Equipment: Hairline processing machine, Polishing and buffering wheel
<Cleaning>
Abrasive powder from previous process is washed away in this process.
After ground by stone and buffer, quite a lot of tiny metal or stone particles are adhered on the blade surface.
Because they are micro-tiny and cannot be washed off by tap water, ultrasonic and environmental friendly detergent are used.
Equipment: Washing and drying machine
<Marking>
Blade is inscribed/marked in this process.
Marking method varies, such as electro-corrosion, press engraving, laser, machine or hand engraving etc.
Electro-corrosion is primarily used for our mass produce items.
Equipment: Marking machine
<Handle Fitting>
Many handles of western style knives are fixed by pressing the rivets from both sides.
On the other hand, blade is just stuck into the handle for traditional Japanese style knives.
It is done by hand of craftsman.
Equipment: Press machine
<Handle Polishing>
It is necessary for fixed rivets handle to be polished carefully in order to smooth the surface of both wood and metal parts.
This process is very important to make comfortable grip.
For stainless steel hollow handles, shot blasting is processed.
This ease the metal texture of handle, and at the same time, it is also good for non-slip effect.
Equipment: Grinding and buffering wheel, Shot blasting machine
<Friction Pressing>
One of the processing methods of forming and pattern making, often used for cutlery manufacturing which is the biggest industry here in Tsubame.
In our factory, this procedure is used for making ribs and patterns on the blade.
Equipment: Friction press machine
<Forging>
Heat up the raw material and hammer to form knife shape.
Metal components become very fine and stable by hammering, and it is eventually going to be durable and quality steel.
Compare with press-out method, advantage of forging is that you can make any shape you would like.
Experience, certain level of technique, and tremendous concentration are required though.
Equipment: Gas furnace, Spring hammer
<Shaping>
Distortion is flattened or corrected in this procedure.
Unused parts are then cut, and it is ground to form shape of the knife.
Handle to be welded in the next procedure, it is then move onto polishing.
Welded part is smoothly polished by using different type of polishing machines.
Equipment: Grinding and buffering wheel
<Laser Cutting>
Blade is cut out of the steel by irradiated laser.
Since shape of the object is exactly the same as the data read by the machine, it is therefore very flexible and capable for wide range of custom made blades.
Equipment: Laser cutting machine
<Heat Treatment>
In order to obtain certain hardness on knife blade, steel is heated and quenched in this procedure.
Metal components are activated by heating, and are stabled by quenching, those components will then be combined firmly and become very hard.
In TOJIRO Knife Atelier, salt bath and electric furnace are used.
Once it is heat treated, blade becomes very firm.
But it is too firm at this stage and it can be broken apart or chipped.
Annealing is then processed with lower temperature to obtain viscosity.
Blade is then become perfect with appropriate hardness and viscosity.
Equipment: Salt bath, Electric furnace, Annealing furnace
<Sharpening>
Blade is edged through sharpening process by using coarse, middle, and fine grit stones. Eventually leather wheel is used to make final polish.
During sharpening, water is used to prevent the blade from tempering by frictional heat, as well as to drain metal particles away in order not to deposit in the stone texture.
Wooden jig is used to improve workability.
Equipment: Sharpening wheel, Grinding and buffering wheel
<Handle Making>
Unlike mass-production type of handles which are supplied by handle makers, here in the TOJIRO Knife Atelier, our craftsmen make handles from raw material.
Handle is cut out from the plank shaped material by band saw. Besides solid wood, artificial materials, such as micarta and pakkawood, are often used.
Equipment: Band saw, Drill, Grinding and buffering wheel
<Carving>
Each knife is carved by a skillful craftsman.
Though there are many ways of marking, such as electro corrosion, stamping, and laser, hand carving is the most impressive and you can feel the passion of craftsmen.
Equipment: Chisel, Hammer, Anvil